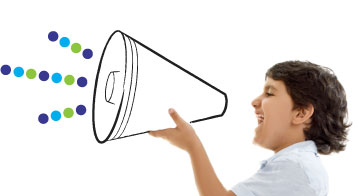
EcoGenerator to najnowsza elektronika
Na instalacji EcoGeneratora nie ma zbyt wielu pracowników, którzy pilnują prawidłowego działania urządzeń lub nimi sterują. Ręczne i mechaniczne systemy odeszły już w niepamięć, bo dziś to wszystko przejęła elektronika. Ta w tak nowoczesnym zakładzie jak EcoGenerator jest na bardzo wysokim poziomie. Zapraszamy do naszej serwerowni.
Kotły, ruszty, pompy, wentylatory, wypychacze, zasilacze… Można wymieniać długo maszyny, którymi steruje się z poziomu komputera. By to było możliwe potrzebnych jest wiele skomplikowanych urządzeń, które w EcoGeneratorze mieszczą się w serwerowni i kilku rozdzielniach.
- Serwerownia to centrum sterownia procesem całego zakładu. - Tutaj znajdują się sterowniki, które zarządzają procesem produkcyjnym – mówi Marcin Gałek, specjalista ds. elektrycznych i AKPiA w Zakładzie Unieszkodliwiania Odpadów w Szczecinie. – Istnieją tylko pojedyncze urządzenia, które mają swoje układy sterowania, ale ogromna większość jest właśnie tutaj.
Sterowniki to niewielkie skrzyneczki z oznaczeniami i świecącymi diodami. To takie przemysłowe „komputery”, w których zawarte jest całe oprogramowanie, logika działania zakładu – jego poszczególnych urządzeń. Program zaszyty w sterowniku steruje urządzeniami wykonawczymi – silnikami, zaworami, pompami, wentylatorami itd. Mamy pięć takich sterowników. Każdy obejmuje jedną część zakładu.
Wszystkie sterowniki, a także towarzyszące im np. zasilacze czy ringi światłowodowe są podwójne. Każdy z nich ma swój drugi odpowiednik, który w razie awarii przejmuje jego funkcję.
Jeden ze sterowników kieruje np. pracą kotła w pierwszej linii spalania – wypychaczami czy pracą samego rusztu. Parametry pracy tych urządzeń są w nim zaprogramowane. Na parametry te może wpływać operator, który obserwuje pracę urządzeń na tzw. wizualizacji komputerowej. Kiedy chce np. by coś pracowało szybciej, przekazuje taką informację inżynierom systemu a ci z poziomu stacji inżynierskiej, mogą modyfikować program. Wykonują to w tzw. bramkach logicznych.
Przeprogramowany sterownik wydaje polecenie, które kierowane jest do specjalnych modułów. Wszystko odbywa się przez kable połączone z danym urządzeniem. By skrócić tę drogę, na terenie zakładu jest kilka rozdzielni z modułami, które są bliżej sterowanych urządzeń. Specjalne moduły nazywane „safety” (z ang. bezpieczne) są dedykowane najważniejszym maszynom. To m.in. kocioł. To moduły, które nie mają prawa zawieść.
Czytaj też: Kryje się za wielkim murem. To "respirator" zakładu
- Potwierdzenie wykonania polecania odbywa się poprzez wysłanie sygnału zwrotnego do sterownika. Operator systemu otrzymuje informację, że polecenie zostało wykonane i np. jakieś urządzenie zostało włączone itp. – dodaje Marcin Gałek.
Znajomość oprogramowania i zrozumienia działania systemu to nie jest sprawa prosta, dlatego, by pełnić funkcję inżyniera systemu należy wykazać się sporą wiedzą z zakresu automatyki przemysłowej.
W pomieszczeniu z elektroniką muszą panować odpowiednie warunki. Optymalna temperatura to ok. 20 stopni Celsjusza, dlatego pomieszczenia są wyposażone w klimatyzację i specjalne wentylatory.
Więcej zdjęć z ECG na naszym Facebooku i Instagramie.